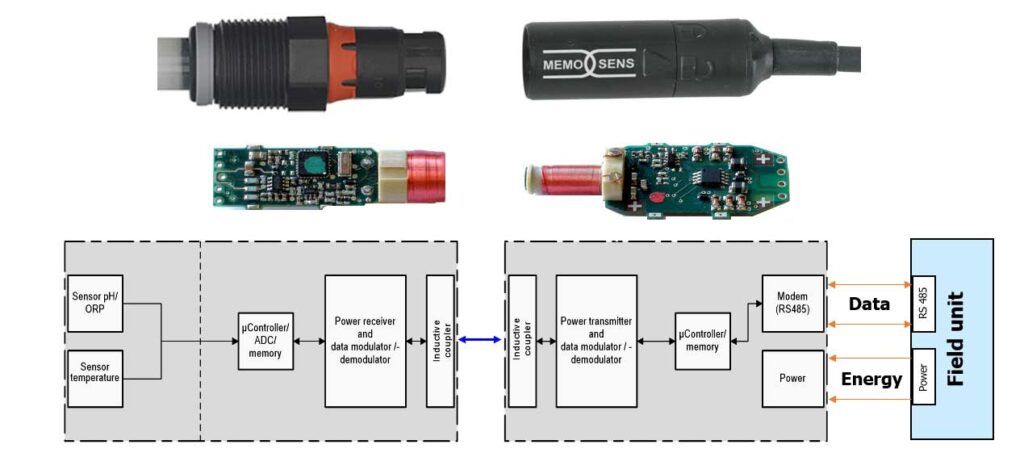
Inductive technology is now widely integrated into various consumer products, enabling data transfer, battery charging, and direct device powering. Its simplicity belies its profound impact. Everyday items like electric toothbrushes, smartphones, and implantable medical devices utilize this technology.
In the industrial sector, inductive technology enhances measurement performance and reduces maintenance time in liquid analytics. The introduction of inductive circuits is having a positive impact on user interaction with liquid analytical products such as pH/ORP, conductivity, and DO sensors. This innovation features a waterproof, quick-disconnect design that promises significant time and cost savings. But how does it work, and why is it so important?
Inductive Circuit – Theory of Operation
An induction coil generates an alternating electromagnetic field, which transfers power and data to a secondary coil. This secondary coil then converts the electromagnetic field back into an electric current.
Benefits of Inductive Technology for Liquid Analytics
- Immune to Moisture
Traditionally, sensor and cable connections have relied on metal components to transfer power and signals between the sensor and transmitter. However, both analog and digital sensors with conductive quick-disconnects are vulnerable to moisture. When metal components are exposed to moisture, the risk of measurement inaccuracies or equipment failures due to corrosion on the connector contacts increases.
In contrast, induction coils use an electromagnetic field to transfer power and data, eliminating the need for metallic contacts. The hermetically sealed coils in the sensor head and cable connection are resistant to moisture and can even be submerged. This unique feature effectively prevents measurement inaccuracies and equipment failures.
- Immune to Electrical Noise and Grounding Issues
Analog technology often faces issues such as signal leakage, electrical interference noise, and ground loops. These problems can cause measurement drift, necessitating frequent calibration and giving the impression that sensors have failed prematurely.
Inductive technology addresses these issues by enabling sensors and transmitters to communicate via a digital RS-485 signal instead of relying on voltage changes. This shift eliminates the noise and grounding problems associated with analogue technology. Consequently, RS-485 communication provides more reliable measurements, reduces the need for frequent calibration, and decreases the frequency of sensor replacements.
- Offline Calibration
For analogue measurements, technicians must calibrate the transmitter, cable, and sensor together. This means they need to bring all necessary tools, spares, and solutions to the measurement site for cleaning and calibration. Environmental exposure of metal sensor and cable connections can lead to faulty calibrations.
Inductive sensors, which are hermetically sealed and have embedded microprocessors, allow for true offline calibrations. Technicians can perform these calibrations in a controlled environment at their convenience. The sensor can then be “hot-swapped” in the field at any time and in any environment.
By eliminating issues caused by moisture and electrical interference, and enabling offline calibrations, inductive technology is revolutionizing online liquid analytics. Users benefit from more reliable measurements and spend less time maintaining and replacing equipment in the field.